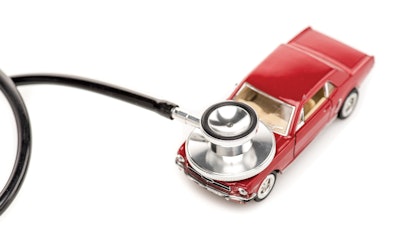
Before I begin, a plethora of people warrant a level of gratitude that words are not enough to express. I won’t name everyone here, to not leave anyone out. Though, to make it clear, SATA Canada and Color Compass Corporation are very fortunate to have some of the best people on the planet working for them, not to mention just being great companies overall. I am forever grateful to all that were there at that moment.
This thing happened to me on the way to work the other day. December 3, 2024, at 8 a.m., I was entering the offices of SATA Canada in Vaughan, Ontario, to set up for a workshop the following day. This workshop never happened, as I was granted the experience of having a heart attack as I walked through the door, a ‘widow maker’ as I was so elegantly informed by a smiling nurse later on.
For those of you in the industry, who, at times, I may offend with my opinions, let it be on the record that I am not done yet. When you are being whisked around the GTA in an ambulance between spurts of idle chit-chat with EMS attendants, you can’t help but think about collision repair and our processes and how they relate. Well, I can’t help it; it may be different for you. I know you’re asking what this has to do with anything ADAS-related because this Collision Repair magazine issue focuses on all things ADAS. Please work with me here.
As soon as the attack began, I was entered into a repair system, much like a vehicle getting towed to a shop. At this point, EVERYTHING was out of my hands. I decided not to question anything and let the system take its intended course of repair. After all, they are the professionals— who am I to question a medical expert with more student debt than the payroll for Manchester United?
First stop, triage—or repair planning. This is where they ask you a variety of questions, do a pre-scan and poke and prod at you to figure out what is damaged and what the repair plan will be. Now, this shop is swamped with a variety of claims, so it takes some time to get sorted. Due to volume, they have different levels of ‘estimating’ taking place. First, it is determined that I am a non-drive and will be staying. The team has created a repair plan involving some internal viewing, a ‘disassembly,’ so to speak; this will occur the following day due to scheduling, equipment, and technician availability. In just showing up, I will have an impact on their WIP. A sublet is determined, and off I go; I need to be on the rack and get straightened out; some measurements take place showing the extent of the damages, they slide me into production, confirm the use of aftermarket parts—no OE available, discontinued—and voila, repairs underway. Once the sublet is complete, it’s back to the shop on file. At this point, everything is all good to go—or so I thought—but one more step: calibrations.
Yes, a post-scan is completed, verifying a few things. There are some historic codes and a few new ones. Based on the OE procedures available, some calibrations will be needed. Fifty-seven years without a scan and no MILs on the dash, who knew?
Now, this facility has state-of-the-art calibration equipment and access to information. It is a vital part of ensuring the repairs are completed up to the OE standards. My guess is they did a lot of research to find out which is most adaptable to their requirements. Would this equipment being used for cardiology be the same for neurology? Likely not. Is there a need for sublets? At times, most definitely; not every repair is the same. Some makes and models have different parameters. A little cleanup detail and final calibrations with a test drive complete, and I am on my way out the door: a seamless, successful repair.
This is where the collision industry and medical industry part ways. I entered this experience completely blind; it was not a planned service call. I felt very reassured and safe letting the medical system process my claim; they are professionals and I found comfort in their abilities; as I said, who am I to question the approach, process, skillset and ability? What I noticed was the attention to time; it was noted that things had to progress quickly, but not so quickly as to cut corners, where confirmation and due diligence were required, the time was taken, and no questions asked. The skill set of each organization member was not to be questioned; they did what needed to be done and disregarded pressure from outside sources. The equipment was maintained and used for its intended purpose by someone who knew how to use it through constant training and professional development. All the OE procedures were followed and explained in detail.
In my opinion, and you are entitled to my opinion, I can write this article today because these people did their job justice with high moral values, ethics, compassion, and professionalism. Now, I cannot account for what takes place behind the scenes or in the lunchroom of a hospital, what I do have is a lived experience.
I have been calibrated and sent on my way in confidence after the repairs were completed. When it comes to ADAS calibrations in our industry, can we say the same? I want to take my vehicle to the place that places the same moral standards and values on their repair process as that hospital does. I want to drive away, knowing deep down all is good. I am not a medical professional, and your customer is not a collision repair professional, so it’s up to the professionals to set things right for the customer. Are we truly doing that?