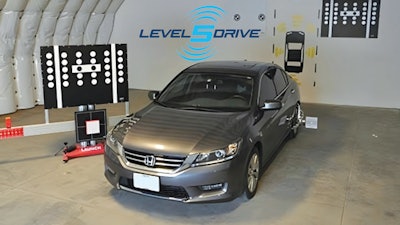
It is a very common belief that the system won’t allow a calibration to occur if any of the requirements are not met, therefore any success report must indicate that the systems will perform as intended. This is absolutely not true.
ADAS...this acronym spells out a great deal of confusion and misunderstanding in our industry.
ADAS systems are complex networks that rely on precise calibration of their sensor suites to function properly. In many cases, a large part of the calibration process involves the vehicle being placed into a specific environment, with the vehicle set in a specific state; with sensors then exposed to specific targets or reflectors located in a specific place relative to some specific part of the vehicle. We might consider this the zero point, or the condition from which all measurements will now be performed. This will include the vehicle calibration measurements, as well as all subsequent measurements performed by the vehicle systems (i.e., detecting things). The calibration routines that are now performed will assume that the environment, vehicle, and targets or reflectors are all in the correct state, or at zero point.
Let’s consider the case of a vehicle requiring lane keep assist camera calibration following installation of a specific brand of aftermarket windshield. The technician knows that a lane-keep assist camera calibration with this particular brand—and it could be any, I’m not referencing any glass manufacturer in particular here, just illustrating a common issue—means you must set the target 15 millimetres lower than it says in the repair manual in order to produce a success report. Can we consider this ADAS system to now be properly calibrated, and relied upon to function correctly through all of it conditions it was designed for? Of course not. Yet, the technician has produced a success report. The technician, perhaps unknowingly, is exploiting the limitations inherent in the calibration software.
The term “success” doesn’t always mean that the system is properly aligned, calibrated and working as intended. Rather, it means that the required minimum threshold has been recognized by the software. As the software by necessity must assume that zero point is correct, it will dutifully assess the calibration conditions and provide the calculated result. In the case of the windshield technician adjusting the target height to accommodate an incorrectly positioned camera in an aftermarket windshield: every measurement performed by the lane-keep assist system will have some degree of error, even if all of the other factors comply with the procedures in the OE repair manual.
The confusion continues as ADAS systems are engineered to be robust and operate under a wide range of conditions. Thus, this system may seem to perform just fine under many conditions but may perform dangerously or not at all under some other conditions. For example, operation during the daily commute might seem fine. Perhaps months go by and then the vehicle is used for a family camping trip. With a full tank of fuel, the whole family on board, and a weekend worth of camping supplies and food in the back, the system might fail to correctly locate the vehicle in the lane, perhaps even causing a crossover into a different lane. Or perhaps it fails to locate the lane marker at all during a moment when the driver is distracted and allows the vehicle to drift into the next lane. Unfortunately, there is no reasonable way to test every vehicle under every operating condition. This is why it is so critical that every ADAS calibration is performed using OE compliant equipment, in the correct environment, with the vehicle in the correct state, faithfully adhering to the procedures in the OE repair manual.
It’s not only aftermarket windshields that can cause false-positive calibration results. These can easily happen when performing calibrations in an improper environment. Not enough space, floors not flat and level as specified by the vehicle manufacturer, lighting not controlled correctly, et cetera, or when the vehicle is not in the correct state; tire pressures/sizes incorrect, suspension modified, cargo inside vehicle. Or when using incorrect targeting, like resized targets to circumvent space requirements; measurements taken from the incorrect locations on the vehicle, target placement changed to suit incorrect sensor placement. Really, anything that deviates from the OE repair manual can create a success report that doesn’t actually indicate a successful calibration.
The repair manual is loaded with statements that may seem unimportant. Especially since the calibration will proceed, apparently successfully, even when the technician ignores some or all of them. Blind spot sensor calibrations, for example, generally require that a minimum area be free of any metal or reflective objects. This is not a handy helpful hint from the vehicle manufacturer. It is a critical element in ensuring that the calibration can be performed without the sensor accidentally picking up a signal from some object other than the intended reflector. Many facilities don’t have such an area available and will perform the calibration with a frame rack, or a lift, or the wall of the building inside of this minimum area.
This, again, can result in a false-positive successful calibration report. As with our previous false-positive windshield calibration, any improperly calibrated ADAS system may appear to function normally when test-driven. This is because of the very large range of conditions that the system is designed for. The error-driven John Marlowe, co-founder of Level5Drive, demonstrates an aftermarket.
system limitations may not be noticed until the vehicle enters an “edge case” condition, where the combination of imminent danger, an error-riddled ADAS system, and an unaware driver may cause a catastrophe, or may fail to prevent or mitigate a collision.
The mistaken notion that the scan tool’s success report definitively indicates a bonafide ADAS system calibration leads to a growing number of vehicles being calibrated using improper equipment, unsuitable environments, and an ever-increasing number of people selling devices specifically designed to cheat or defeat ADAS system calibration software with the sole purpose of producing a success report.
ADAS systems, when properly calibrated, can enhance road safety immediately and directly. Drivers quickly adapt to these systems and come to rely on them. ADAS systems, when improperly calibrated, may have limited or no safety value. Worse, some systems can take control of some vehicle functions and could directly cause damage, injury, or even death if they are not operating correctly.
If you’re performing ADAS calibrations, it is critical to not only ensure that you are faithfully adhering to the OEM procedures, but that you are also fully documenting this. If you have an ADAS partner performing these operations for you, you really need to ensure that they are following the correct procedures and fully documenting that they have done so.
A success report from a scan tool isn’t going to save lives. Properly performed ADAS calibrations will.