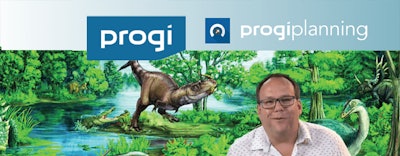
BY JULIA LLOYD AND ALLISON ROGERS
Running a well-oiled collision centre can be challenging—but Progi has a solution. Last week, Charles Aubry, account manager at Progi took the CCIF virtual stage to discuss how the ProgiPlanning software, combined with a capacity planning mindset, can help collision repair facilities establish a capacity-planning ecosystem. ProgiPlanning is more than software—it’s a state of mind.
With ProgiPlanning, collision centres simply enter their goals and targets to open up a world of optimization. The software is used as a visual to help shops stay on course and see where improvement can be made by tracking important key performance indicators (KPIs) such as daily, weekly and monthly loads and targets, cycle times, overall productivity, hours produced per tech and more.
“With ProgiPlanning, what you can see, you can achieve,” Aubry told the CCIF audience. While the ProgiPlanning software itself can provide data to help facilities better manage their goals and targets, Progi says any facility can adopt its capacity-planning mindset and tackle a seven-step strategy to achieve top performance, even without implementing the software.
When first adopting the ProgiPlanning mindset, a collision centre must establish its targets. Using ProgiPlanning, facilities can help find and track their chosen KPIs like margins, gross sales and key-to-key cycle time. Furthermore, the software can also produce hours sold produced per tech in a given period of time in any given period (like week or month) to help the team stay on track.
Aubry suggests that collision centres sit down and think about their desired performance in this stage.
“Define your desired performance and establish your objectives,” he said. “Remember, they must be realistic and time-bound to be successful.”
Next, the collision centre must ensure all members of the team are on board. Without clear, cohesive communication about goals and targets, there is no team, said Aubry. “Communication is as important as the water needed to grow a plant. The better you control your communications, the better you can control your success.”
The third rule in sticking true to a ProgiPlanning mindset, involves maintaining and analyzing your operations. If you are not reaching your objective, said Aubry, you will need to investigate what factors are blocking your path.
When it comes to bottlenecks in the painting process, parts flow and the quality of estimates leading to interruptions in the repair process, knowing how your chosen KPIs behave and observing any patterns is a key part in reaching a capacity-oriented objective.
Fortunately, the ProgiPlanning software can easily provide critical data and visual reports to help collision centres better understand where they may be missing the mark on their goals. While it may be tempting to take on all you can manage to reach top performance, this is not an effective strategy. Aubry said the secret to capacity planning is to be loaded at maximum capacity while simultaneously remaining efficient. If a collision centre overloads the system, serious operational problems could occur and result in lower performance, sending the team back to the drawing board.
ProgiPlanning can be a lifesaver when it comes to managing daily, weekly and monthly workloads. The tool can provide a colour-coded schedule to indicate daily workloads in percentage.
Aubry also suggested collision centres keep an eye on their work-in-progress (WIP) numbers to determine how much your facility can take on before its efficiency is challenged. Another element of this step is to plan repairs “at the best possible moment,” said Aubry. Once your facility understands its workload and cycle times, you can begin scheduling repairs at opportune times to maximize efficiency. This means your collision centre should be receiving and delivering vehicles every single day. The dated method of receiving all your vehicles in on Monday and holding your breath until Friday is a surefire way to run into bottlenecks.
“Understanding scheduling is a fundamental rule in optimizing your productivity and becoming a pro capacity planner,” said Aubry. ProgiPlanning uses a severity grid to indicate the most opportune time to position work in weekly schedules. Each collision centre has its own customized grid, and Progi says its “champion users” even go as far as setting seasonal grids to adapt their schedules with the jobs currently available in the market. Once you have the aforementioned steps under your belt, Progi has just one more rule— challenge your limits.
“Do you want to go further? Are you able to do better? If the answer is yes, you will have to challenge your ecosystem again and find even better ways to plan your capacity,” said Aubry. However, that does not mean you should spend too much time comparing “apples with apples,” said Aubry.
“Compare yourself with shops of the same size and accept that you may not be at your top yet. Don’t be jealous—be inspired.” To learn more about Progi, or the ProgiPlanning software, visit progi.com.
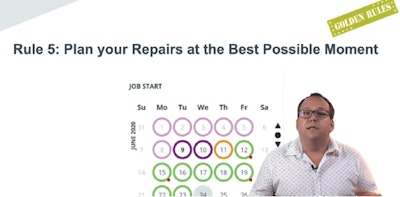
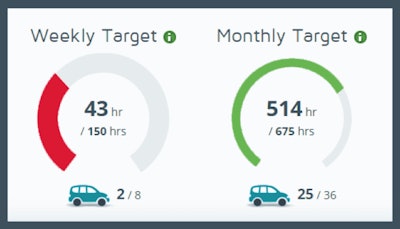