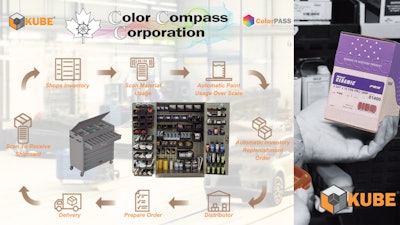
Transforming business intelligence for smarter decision-making
Navigating the complexities of the collision repair industry can be challenging, but KUBE® Inventory Management simplifies inventory control, making it organized, reliable, and profitable.
Here’s how KUBE® can transform the Collision Repair operations:
Business Intelligence:
KUBE® Inventory Management is built-in analytics eliminating guesswork, providing essential insights to drive performance and profitability. Kube® operates based on pre-determined minimum and maximum inventory levels, with orders placed on specified days each week. The system runs weekly orders, helping control costs through data review and KPI comparison.
Superior Organization and Performance:
• KUBE® Cabinets: Customizable, heavy-duty cabinets designed for collision repair facilities, allowing for scalable and organized inventory, even in a tight shop footprint.
• Smart Scanner: Advanced barcode scanning technology for effortless and instant capture, designed for rugged shop environments. You get instant and effortless point-and-shoot capture of any electronic or printed barcode in virtually any condition — no aiming and no waiting. The KUBE® scanner features all-day power and is designed for a rugged shop environment.
• ColorPass: Interfaces with colour software and smart-scales to track liquid consumption and place orders automatically. Fully automated paint consumption by mixing on the scale. Easy and intuitive, works with all major paint manufacturers.
• The Clips & Fastener Program: This program provides high-quality clips & fasteners essential for vehicle repairs, ensuring these components are always in stock, avoiding delays, and maintaining high standards. Integration with KUBE® Inventory Management streamlines inventory management and ensures accurate billing, making the repair process smoother and more efficient.
Advanced Analytics:
• KUBE® Analytics Packages: Powerful and intuitive business analytics offers fundamental inventory tracking and consumption monitoring. KUBE® reporting features include immediate inventory valuation, material consumption tracking by department and technician, and indicators for inactive and redundant inventory.
• KUBE® Dashboards: Enhanced visual analytics track consumption per technician and repair order, offering real-time snapshots of material use and profitability. Key Performance Indicators by KUBE® include material cost as a percentage of sales and gross profit, average cost per RO, cost per employee per hour produced, materials used per RO, as well as highlighting lost opportunities for sales.
• KUBE® Clips & Fastener Program: This program provides high-quality clips and fasteners essential for vehicle repairs, ensuring these components are always in stock, avoiding delays, and maintaining high standards. Integration with KUBE® streamlines inventory management and ensures accurate billing, making the repair process smoother and more efficient.
Voices from Industry:
Examples can be colour tinting training, if too many spray out cards are logged then spray out training is required if too many jobs need to be redone.”
He also highlights the impact on customer satisfaction: “We have greatly reduced material costs in the shop and have been able to always have material there when needed. I always recommend it to any shop owner I speak to because you really don’t know how much money you are truly losing until you have a great system to track it.”
Key Features:
• Automated Supply Chain: KUBE® automates your supply chain, tracking consumption, usage, and profitability at every level. Automated product setup and price matching including easy scanning and automated receiving.
• Weekly Orders: KUBE® Inventory Management sets order days and run orders weekly based on pre-determined minimum and maximum inventory levels with live on hand Inventory.
• Cost Control: KUBE® will utilize data for review and KPI comparison to drive behavior and profitability. Fully automated paint consumption tracking and comprehensive tracking and reporting by department, technician, and repair order. Secured cabinet access for inventory control with an audit trail option.
• Supplemental Invoicing: For any additional materials used that are not included in standard material allowance, Kube can generate supplemental invoices. This ensures that all extra costs are accounted for and billed appropriately. KUBE® Inventory Management is the essential tool for any collision repair facility aiming to enhance performance and profitability through superior organization and advanced business intelligence.
Are you ready to elevate your auto collision repair business? Discover the power of KUBE® Inventory Management today and experience the future of collision repair management. Feel free to reach out to Color Compass Corporation at www.colorcompass.com/contact/.