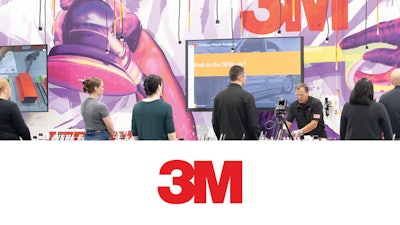
Sustainability, in a collision centre involves reducing the amount of time, products, labour and energy needed to complete a repair, including reducing or eliminating rework. This also contributes to increased profitability.
This starts with defining new processes and implementing those new standards throughout the shop with a shared vision.
DEFINE A NEW PROCESS
The training at the 3M Skills Development Center is process driven and product agnostic. Processes are designed and set that collision centres can implement to enhance sustainability benefits without breaking the bank. In fact, it’s a common misconception that by trying to improve its sustainability, the collision center will be negatively impacted financially with additional costs or process changes that are too difficult to implement.
Here are a few improvements to put in place to get started with your eco-friendly goals.
Keep the paint booth contaminate free. Cleaning the booth each morning will limit the possibility of additional labour and materials for the painter and the detail department. A clean paint job can help increase productivity by lowering the additional labour required to compound out the imperfections and reduce the amount of materials used.
A dust extraction upgrade in each department will help reduce dust in the shop and can help extend the life of your abrasives. Instead of blowing repairs off with a hand blower, using a vacuum system will help reduce the amount of contaminates that could later impact the refinish process. Workplace conditions are also enhanced using a dust extraction system due to the reduction of contaminates in the air.
CREATING SOPS
One of the best ways to encourage adoption of a new process is through the implementation of SOPs. A well written SOP for each step of the collision repair is crucial to be successful when implementing process change. The SOP should make the steps clear to all parties involved on what is expected of each role while being simple and easy to understand.
Here are a few SOPs that can really make a difference.
1. ESTIMATOR SOP
The estimator and the blueprinter need to work together to write a complete repair order to avoid delays in the repair process. They should also review the repair with the assigned body tech for a final assessment to reduce the likelihood of missed items and to identify hidden damage.
2. BOOTH SCHEDULE SOP
One of the simplest and most beneficial SOP is a booth schedule. This could be in the form of a white board or digital display in the shop that lists the jobs that need to be completed that day. This board should be filled out with the painter and production manager together each day with the desired order of completion. This will help production to keep moving forward with limited interruptions.
The production manager will not need to interrupt the painter as they will be able to see the progress of each job with just a glance at the board.
BENEFIT OF NEW EQUIPMENT
Reducing energy usage during the repair process is one way to be environmentally responsible. This can be accomplished with the use of short or medium wave curing lamps for urethane primer or the use of a UV primer, which can greatly increase productivity by cutting dry times by more than 75 percent.
REINFORCEMENT TRAINING
Introducing new products supported by new processes leads to the most crucial part of creating a long-lasting and successful program: training. The Skills Development Center at 3M is focused on providing meaningful training across the collision centre -- from the front office staff through the back of the shop to painters and estimators. Investing in your staff to train on new processes is worthwhile to maximize the return on these sustainability- focused changes. Regular training also displays management’s commitment to employees and their individual success.
EXPECTATION OF IMPLEMENTING SUSTAINABLE PROCESSES
Maximized efficiency in each department can help drive profitability by potentially gaining a booth cycle. The average shop today does three to four booth cycles per day, and with proper implementation of SOPs, they may be able to add an additional booth cycle all while reducing material and energy consumption.